The recent criticisms leveled at Boeing by the leaders of United Airlines and Alaska Airlines highlight the severity of the manufacturing problems that have resulted in the grounding of over 140 aircraft.
The discontent expressed by Alaska Airlines CEO Ben Minicucci and United CEO Scott Kirby underscores the deep frustration and disappointment felt by these industry leaders.
Their strong words, delivered in a public forum, signify the seriousness of the situation and the urgent need for Boeing to address the issues at hand.
In a recent interview with “NBC Nightly News,” Ben Minicucci of Alaska Airlines did not mince words, expressing his anger and demanding that Boeing take concrete steps to enhance its in-house quality programs.
This pointed criticism reflects the significant impact that Boeing’s manufacturing problems have had on the operations and safety of Alaska Airlines’ fleet.
The incident involving the door plug of a Boeing 737 Max 9 jetliner, which led to the grounding of these aircraft, serves as a stark reminder of the real-world consequences of manufacturing deficiencies.
Similarly, Scott Kirby of United Airlines emphasized the need for Boeing to take tangible actions to restore its once-stellar reputation for quality.
His call for “real action” underscores the gravity of the situation and the imperative for Boeing to address the ongoing manufacturing challenges.
The financial impact of the grounding of United’s 79 Max 9s further underscores the tangible consequences of Boeing’s manufacturing issues, with the airline anticipating financial losses in the first quarter of the year.
Boeing’s response, announcing a halt in production at its 737 factory to focus on quality, is a step in the right direction.
However, the airline industry and the broader public will be closely watching to see how Boeing follows through on its commitment to addressing these critical issues.
The grounding of the Max 9s and the subsequent investigations into the causes of the incident have brought the spotlight squarely onto Boeing’s manufacturing processes, highlighting the need for comprehensive and lasting solutions.
The broader implications of these manufacturing problems extend beyond the immediate operational and financial impacts on the airlines involved.
They raise questions about the robustness of Boeing’s quality control measures and the long-term implications for the company’s standing in the aerospace industry.
As one of the leading aircraft manufacturers in the world, Boeing’s ability to swiftly and effectively address these challenges will be closely scrutinized by industry stakeholders, regulators, and the flying public.
In conclusion, the forceful criticisms leveled at Boeing by the leaders of United Airlines and Alaska Airlines underscore the severity of the manufacturing problems that have led to the grounding of a significant number of aircraft.
The demands for tangible improvements in Boeing’s quality programs and the expressions of frustration and disappointment reflect the urgency of the situation.
The aerospace industry will be closely monitoring Boeing’s response and actions in the coming months as it seeks to address these critical manufacturing challenges.
In recent years, the global aviation industry has been marred by the detrimental effects of manufacturing flaws, notably impacting the delivery schedule of Boeing’s flagship aircraft, including the Max jets and the 787.
The repercussions of these delays have reverberated across airlines, with United Airlines receiving a significantly reduced number of Boeing aircraft compared to their initial projections.
This essay aims to delve into the multifaceted ramifications of these manufacturing flaws on the aviation industry, particularly focusing on the implications for airlines, the challenges faced by Boeing, and the broader repercussions on the competitive landscape.
United Airlines, a prominent player in the aviation sector, has been grappling with the ramifications of the delayed delivery of Boeing’s Max 10 jets, a larger iteration of the Max line.
The protracted certification process by the Federal Aviation Administration (FAA) for the Max 10 and its smaller counterpart, the Max 7, has resulted in a significant setback, disrupting United’s strategic growth plans.
With the Max 9 jets also facing grounding, United’s President, Scott Kirby, expressed apprehension, stating that the situation could potentially impede the airline’s expansion plans.
This predicament underscores the profound impact of manufacturing flaws on the operational and strategic trajectories of major airlines, compelling them to reconsider their fleet acquisition and growth strategies.
Similarly, Alaska Airlines, which had initially intended to procure Max 10s, now finds itself at a crossroads due to the prevailing uncertainties.
The airline’s Chief Executive Officer, Ben Minicucci, emphasized the need to reassess their long-term fleet composition in light of the evolving circumstances.
This underscores the pivotal role of adaptability and strategic agility in navigating the challenges posed by manufacturing flaws, as airlines are compelled to realign their procurement strategies to mitigate the repercussions of delayed deliveries and grounding of aircraft models.
Amidst these challenges, Boeing’s commercial airplanes division, led by CEO Stan Deal, has issued a formal apology for the disruptions caused by the grounding of the Max 9 jets.
Acknowledging the adverse impact on airline customers, employees, and passengers, Deal underscored the company’s commitment to implementing a comprehensive plan to rectify the situation, ensuring the safe resumption of the affected aircraft and enhancing overall quality and delivery performance.
This proactive stance by Boeing reflects the imperative for industry leaders to address manufacturing flaws swiftly and decisively, underscoring the criticality of maintaining customer trust and operational integrity.
Furthermore, the competitive dynamics within the aviation industry have been significantly influenced by these developments.
The reliance on a limited number of global manufacturers for large aircraft, notably Boeing and its European counterpart, Airbus, underscores the intricate interplay of supply chain disruptions, market demand, and competitive positioning.
The repercussions of manufacturing flaws extend beyond individual companies, permeating the broader industry landscape and shaping strategic decisions related to fleet acquisition, growth projections, and operational resilience.
In conclusion, the persistent manufacturing flaws affecting Boeing’s aircraft deliveries have engendered a ripple effect across the aviation industry, impacting airlines, manufacturers, and the competitive landscape.
The challenges faced by United Airlines and Alaska Airlines underscore the imperative for adaptability and strategic recalibration amidst unforeseen disruptions.
Boeing’s proactive measures to address the situation reflect the pivotal role of industry leaders in mitigating the impact of manufacturing flaws and upholding operational integrity.
As the aviation sector navigates these challenges, it is imperative for stakeholders to collaborate, innovate, and prioritize safety and reliability to surmount the repercussions of manufacturing flaws and sustain the industry’s long-term viability.
The recent developments at Boeing’s 737 factory in Renton, Washington, have sparked discussions and raised concerns regarding the quality control procedures in the aviation industry.
The company’s initiative to conduct working sessions focused on quality, along with increased oversight by regulatory bodies, has brought attention to the critical aspects of manufacturing and safety standards in commercial-plane production.
This essay aims to analyze the implications of these events on Boeing, its stakeholders, and the broader aviation industry.
Boeing’s decision to hold working sessions dedicated to evaluating and improving their manufacturing processes is a commendable step towards ensuring the quality and safety of their aircraft.
By providing production workers with the opportunity to pause, reflect, and make recommendations for improvement, Boeing demonstrates a commitment to addressing any potential shortcomings in their operations.
This proactive approach to quality control is essential for maintaining the company’s reputation and regaining public trust, especially in the aftermath of previous incidents involving the Max line of planes.
The heightened oversight by the Federal Aviation Administration (FAA) and the ongoing investigations into the quality procedures of Boeing and its suppliers, particularly Spirit AeroSystems, underscore the significance of adherence to stringent manufacturing standards.
The focus on quality assurance and compliance with regulatory requirements is pivotal in ensuring the airworthiness and safety of commercial aircraft.
The National Transportation Safety Board’s investigation into the recent accident involving an Alaska jetliner further emphasizes the need for thorough scrutiny and accountability in the aviation industry.
The troubled history of Boeing’s Max line of planes, marked by tragic crashes in 2018 and 2019, has had far-reaching implications for the company and the aviation sector as a whole.
The incidents, which resulted in the loss of 346 lives, exposed critical flaws in the automated flight-control system of the Max 8 aircraft.
The subsequent grounding of all Max jets worldwide for 20 months, coupled with the scrutiny from congressional investigators, highlighted the need for comprehensive safety measures and robust regulatory oversight.
The financial impact of the Max 9 grounding on airlines such as United Airlines Holdings Inc. and the subsequent market response reflect the interconnectedness of the aviation industry.
While the initial decline in Boeing’s stock was modest, the positive outlook for United Airlines and Alaska Air Group demonstrates the significance of the Max line’s operational status on the financial performance of key industry players.
This interplay between manufacturing quality, safety, and financial outcomes underscores the complex dynamics within the aviation sector.
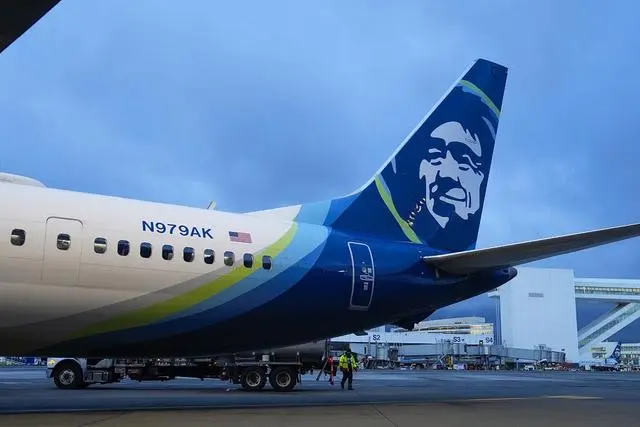
The events surrounding Boeing’s 737 factory and the implications for the aviation industry extend beyond the immediate concerns of a single company.
They prompt a broader discourse on the critical intersection of quality control, safety standards, regulatory oversight, and financial implications within the aviation sector.
The need for continuous improvement, transparency, and collaboration among stakeholders is paramount in fostering a culture of safety and reliability in commercial aviation.
The recent developments at Boeing’s 737 factory in Renton, Washington, and the subsequent investigations and market responses underscore the multifaceted nature of challenges facing the aviation industry.
The emphasis on quality control, regulatory oversight, and the financial implications of operational disruptions highlights the interconnectedness of manufacturing, safety, and market dynamics.
As Boeing and the broader aviation sector navigate these challenges, a concerted effort to prioritize safety, compliance, and continuous improvement will be essential in shaping the future of commercial aviation.
In conclusion, the events at Boeing’s 737 factory serve as a catalyst for introspection and action within the aviation industry, emphasizing the imperative of upholding rigorous quality control and safety standards to ensure the trust and confidence of passengers, airlines, and regulatory authorities.